,allowExpansion)
Lessons Learned From Functional Safety Standards
Security Standards for Embedded Products
When developing safety critical systems functional safety standards are defined. There are several standards to choose from – for example ISO26262 for road vehicles, IEC61508 for different industries and DO-178B/DO-178C in avionics. However, for non-safety critical product development, there is no universal approach in order to ensure product quality.
Using the full functional safety standards for non-safety critical embedded products is not nescessary. Nevertheless, it makes sense to look into them when setting up design guidelines to implement general approaches.
ISO 26262: Lifecycle of Functional Safety
ISO26262 outlines the whole lifecycle of the product development. It starts with the management of functional safety and goes from concept phase over development and supporting processes into production, operation and decommissioning.
Development Organisation and Supporting Processes
ISO26262 specifies the main pillars of safety culture:
The software development process
ISO26262 covers a wide range of failures which are not relevant for normal development processes. However, Code Coverage, Detecting Issues in the Code, Diagnostic Capabilities, Verification methods and software testing are lined out as well.
Concept Reply highlights the most important aspects and mixes it with additional advice – for example the advantage and disadvantage of reusing code from different projects.
Testing
Testing is usually one of the largest parts of the development process. It is separated into the general types Acceptance Testing, System Testing, Integration Testing and Unit testing. For catching bugs as many cheap ways as possible should be used. To note here is the fact that the quality of software increases with each level of testing.
Concept Reply outlines several chanllenges in the testing process and explains organizational counter actions learned from functional safety standards.
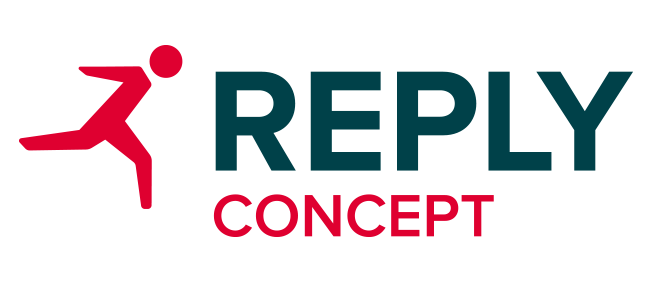
Concept Reply is an IoT software developer specializing in the research, development and validation of innovative solutions and supports its customers in the automotive, manufacturing, smart infrastructure and other industries in all matters relating to the Internet of Things (IoT) and cloud computing. The goal is to offer end-to-end solutions along the entire value chain: from the definition of an IoT strategy, through testing and quality assurance, to the implementation of a concrete solution.